Tối ưu hóa kích thước cổng và vị trí trong khuôn ép phun kem dưỡng da thông qua phân tích dòng chảy khuôn bao gồm một quá trình mô phỏng, phân tích và điều chỉnh thiết kế có hệ thống. Dưới đây là hướng dẫn từng bước để đạt được tối ưu hóa này:
1. Xác định mục tiêu và tiêu chí của dự án:
- Hãy bắt đầu bằng việc xác định rõ ràng mục tiêu, tiêu chí của khuôn phun lotion dạng bơm. Xem xét các yếu tố như chất lượng bộ phận, thời gian chu kỳ, mức sử dụng vật liệu và hạn chế về chi phí.
2. Thu thập dữ liệu quan trọng:
- Có được dữ liệu vật liệu chính xác cho loại nhựa cụ thể sẽ được sử dụng trong quá trình ép phun. Điều này bao gồm chỉ số dòng chảy tan chảy (MFI), độ nhớt, tính chất nhiệt và các đặc tính vật liệu khác.
3. Tạo mô hình:
- Tạo mô hình 3D chi tiết của bộ phận bơm lotion và khuôn phun, bao gồm khoang, lõi, kênh làm mát và hệ thống ray. Đảm bảo rằng mô hình thể hiện chính xác các điều kiện sản xuất dự kiến.
4. Thiết lập mô phỏng:
- Sử dụng phần mềm phân tích dòng khuôn để thiết lập mô phỏng. Xác định các thông số của quá trình ép phun, chẳng hạn như áp suất phun, cấu hình nhiệt độ và tốc độ làm mát. Chỉ định vị trí cổng và kích thước cổng ban đầu.
5. Chạy mô phỏng ban đầu:
- Chạy mô phỏng dòng chảy khuôn ban đầu với vị trí và kích thước cổng đã chọn. Phân tích kết quả, bao gồm thời gian lấp đầy, phân bổ áp suất, đường hàn và vị trí bẫy khí. Xác định bất kỳ vấn đề hoặc lĩnh vực tiềm năng nào cần cải thiện.
6. Phân tích vị trí cổng:
- Đánh giá sự phù hợp của các vị trí cổng được lựa chọn. Xem xét các yếu tố như lấp đầy các lỗ rỗng một cách cân bằng, tránh các khuyết tật về mặt thẩm mỹ và giảm thiểu tác động của các đường hàn. Điều chỉnh vị trí cổng khi cần thiết.
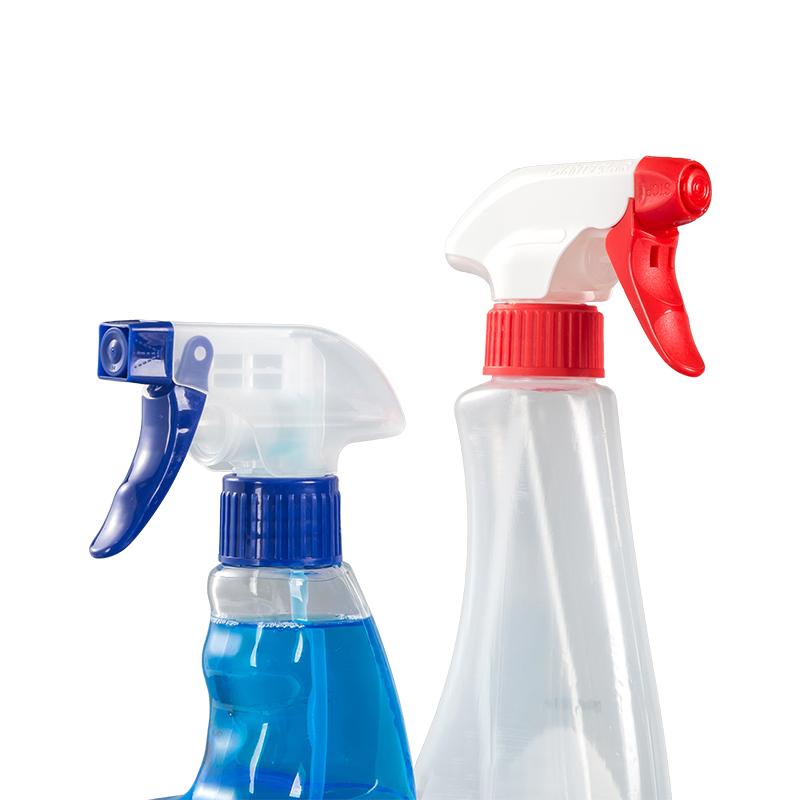
7. Phân tích kích thước cổng:
- Phân tích ảnh hưởng của kích thước cổng đến quá trình tiêm. Tăng hoặc giảm dần kích thước cổng trong các mô phỏng tiếp theo để tìm ra kích thước tối ưu giúp cân bằng thời gian lấp đầy, áp suất và dòng nguyên liệu mà không gây ra lỗi.
8. Lựa chọn loại cổng:
- Tùy theo kết quả phân tích kích thước cổng mà chọn loại cổng phù hợp như cổng rót, cổng cạnh, cổng quạt. Loại cổng ảnh hưởng đến cách vật liệu đi vào khoang và có thể ảnh hưởng đến chất lượng bộ phận.
9. Tối ưu hóa hệ thống người chạy:
- Tối ưu hóa thiết kế hệ thống ray để đảm bảo phân phối vật liệu đồng đều tới tất cả các khoang. Điều chỉnh kích thước và cấu hình đường dẫn để giảm thiểu lãng phí vật liệu và giảm áp suất.
10. Phân tích kênh làm mát:
- Đánh giá ảnh hưởng của vị trí, kích thước cổng đến hiệu quả làm mát. Đảm bảo rằng cấu hình cổng đã chọn không ảnh hưởng đến hiệu quả của các kênh làm mát. Điều chỉnh vị trí kênh làm mát nếu cần thiết.
11. Mô phỏng lặp lại:
- Thực hiện mô phỏng lặp lại, điều chỉnh dần dần vị trí và kích thước cổng dựa trên kết quả phân tích. Tiếp tục tinh chỉnh thiết kế cho đến khi đáp ứng được các tiêu chí mong muốn, chẳng hạn như lấp đầy cân bằng và khiếm khuyết tối thiểu.
12. Xác thực cuối cùng:
- Tiến hành phân tích dòng khuôn cuối cùng để xác nhận kích thước và vị trí cổng được tối ưu hóa. Xác nhận rằng thiết kế đáp ứng các mục tiêu và tiêu chí dự án được xác định trước.
13. Tài liệu và Báo cáo:
- Ghi lại kết quả, bao gồm cấu hình cổng đã chọn, dữ liệu mô phỏng và mọi điều chỉnh thiết kế. Chuẩn bị một báo cáo tóm tắt quá trình tối ưu hóa và kết quả của nó.